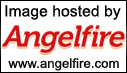
Behind every Metro is a £300 million investment in the most advanced car production methods in the world. The specially built body assembly plant-bigger than 40 football pitches put together-houses a fully computerised production process, where robot machines operate within precise and constant tolerances. Dimensional and structural quality is continuously monitored electronically and is double checked at computer inspection stations; indeed the automatic fault diagnostic equipment built into the Metro assembly lines is the most sophisticated of its kind in the entire car industry. If the slightest deviation from production tolerance is detected, that car is diverted off the line for immediate rectification and re-inspection, a no-compromise system which ensures that every single Metro leaving the factory meets the most critical quality standards ever devised for a volume production car. For the Metro owner, the advantages of microprocessor-control led robots and computer inspectors are very real. Every floor panel, every body panel, every part-assembled section offered to a rob6t multi-welder has to be consistently the right shape, consistently the right size. The machine will accept nothing less. By their uncompromising acceptance attitude, robot machines automatically maintain extremely high quality standards. The drive for quality extends to the Metro's gleaming paint finish, which is more-so much more-than skin deep. No less than 27 separate processes are involved. After the bare metal has been pre-cleaned, it passes through nine stages of pre-treatment sprays and dips and every surface is zinc primed. It then goes through a 7-stage electro-coating and oven-baking process, at which time all the box sections are injected with wax, to minimise corrosion, and special sealant is applied to all body panels which are bolted together. In the next 3-stage process, the entire underfloor area is meticulously undersealed by twin robots. Next, in the sealer spray booths, two coats of grey sealer are applied, first automatically, then by hand. After oven-curing and cooling, the bodies are conveyed to the Finishing Department where, to achieve the Metro's superb finish and its high resistance to chipping, two coats (three on metallics) of thermo-etting colour acrylics are applied. Quality through and through - that's Metro. As the cutaway illustration opposite shows, the Metro's cleanly styled body conceals a wealth of advanced technical features, from which stems much of the car's unique character. The key shows the benefits derived from this hidden technology. Comfort & Refinement. No other hatchback and few medium-size saloons offer such a quiet, comfortable and refined ride as the Metro. Fuel Economy. Petrol costs are a growing problem and much of the Metro's design and development programme has been devoted to keeping them to a minimum. Every Metro is remarkably fuel-efficient and one model-the HLE -is a real fuel economy specialist, in AA tests it achieved 62 mpg at 50 mph. Low Running Costs. Unlike all other hatchbacks- European or Japanese-the Metro needs servicing only once a year, or every 12,000 miles, with no 'short services' or interim checks. Add the other money-saving benefits-low fuel consumption, inexpensive parts, low insurance rating and Supercover-and you'll appreciate that Metro running economy is quite unrivalled. Safety. Metro keeps you out of trouble through precise steering, dual line braking, excellent handling and superb driver visibility. At the same time, you and your family enjoy the added protection of a rigid passenger safety cell, with the fuel tank and steering column located to give maximum security on impact.   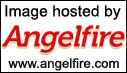 |